Additive manufacturing of self-supported carbon-transition metal compound electrodes is crucial for enhancing water splitting processes for sustainable hydrogen production. To overcome interfacial bonding issues, our study introduces a novel fabrication of carbon-metal phosphide electrodes, yielding efficient water splitting results. Nitrogen and cobalt-rich scaffolds were produced via extrusion-based printing with chitosan-zeolitic imidazolate framework (ZIF) ink, which, upon pyrolysis, converted into nitrogen-doped carbon frameworks that anchored Ni-Co-P nanosheets. Optimizing ZIF-67 in the ink modulates Ni-Co-P density, and via integration with the symmetric triblock copolymer, polyethylene oxide-polypropylene oxide-polyethylene oxide (P123), mesoporosity was created, forming a hierarchical porous structure that facilitated swift mass, charge, and ion transport, and promoted site accessibility. Electrochemical testing revealed overpotentials of 57 mV at −10 mA cm−2 and 263 mV at −500 mA cm−2 for the hydrogen evolution reaction, withstanding 1000 h of cycling at −10 mA cm−2. The oxygen evolution reaction exhibited an overpotential of 163 mV at 10 mA cm−2, and 260 h of cycling durability, outperforming traditional nickel foam electrodes. Functioning both as anode and cathode, the electrode attained a voltage of 1.43 V at 10 mA cm−2, maintaining stability for over 200 h. This research contributes significantly to the practical application of additive manufactured electrodes in energy conversion/storage, environmental, and electronic fields, marking a significant advancement in the domain of green energy technologies.
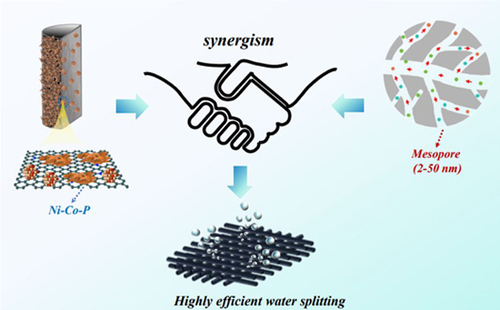
Introduction
Electrochemical water splitting offers a sustainable pathway for producing “green hydrogen,” a pivotal alternative to fossil fuels and a vital resource for various industrial applications such as fertilizer production, petroleum refining, and hydrogenation.1 This process involves the hydrogen and oxygen evolution reactions (HER/OER), necessitating efficient electrocatalysts like Pt/RuO2 to enhance sluggish kinetics and reduce overpotential.2 Traditional powdery electrocatalysts face drawbacks, prompting the development of self-supported electrodes. These electrodes integrate with active sites on conductive substrates to eliminate the need for postcoating processes and binders.3 Transition metal compounds integrated into metal substrates like metal foam (Ni/Cu), mesh (Ti/Cu), plate (Ti), and foil (W/Mo/Cu), as well as fluorine-doped tin oxide (FTO), have been utilized to construct self-supported electrodes.4–8 These metal substrates can rivet high loading of active components, and the seamless contact between catalytic materials and substrates ensures improved electron transfer and mass diffusion, while the tight integration prevents catalyst shedding. Nevertheless, carbonaceous substrates, favored for their cost-effectiveness, flexibility, and corrosion resistance compared to metals, pose a challenge in integration with transition metal compounds.9–11 Unlike polymers, which offer rich functionalities and facilitate component integration due to their proximity to metal surfaces, carbonaceous electrodes face difficulties in this regard. This underscores a critical challenge within the field—the complex integration of carbonaceous substrates with transition metal compounds. Overcoming this obstacle is essential for advancing the development of efficient self-supported electrodes.
To address this challenge, researchers have conducted in situ growth of transition metal compounds such as Co-S, Fe40Co40Se20, MnCo3O4, and NiFe on carbon paper and carbon cloth, aiming to construct self-supported electrodes.12–15 Nitrogen-containing agents (e.g., urea, NH4F, hexamethylenetetramine) are commonly utilized to enhance carbon surface wettability and act as “traps” to capture more metal sites. However, these flexible three-dimensional (3D) frameworks typically exhibit disordered scaffolds with randomly distributed pores, leading to reduced mass transport and high tortuosity. Alternatively, extrusion-based 3D printing holds promise for fabricating self-supported carbonaceous electrodes with hierarchical pores such as uniform macroscaffolds with ordered mesopores, facilitating rapid mass and charge/ion transport rates. Well-developed inks with shear-thinning and viscoelastic properties, including graphene oxide, carbon nanotube (CNT), and carbon black serve as the carbonaceous supporting media and enable the creation of complex structural forms.16–18 Although the use of thermoplastic binders like insulating acrylonitrile-butadiene-styrene (ABS) and polylactic acid (PLA) ensures mechanical integrity, they reduce conductivity and consequently the electrochemical activity of electrodes.19 Deposition of metallic materials (e.g., Au, Pt, and Pd) or the introduction of conductive poly(ortho-phenylenediamine) (PoPD) into carbonaceous electrodes can mitigate this activity-integrity trade-off.20,21 Nevertheless, the weak adhesion of the carbonaceous matrix results in very low loading of active materials. Consequently, constructing self-supported carbon-based electrodes equipped with hierarchical pores and dense transition metal compounds remains a significant challenge. This highlights the need for innovative solutions to address these scientific challenges and advance the field of electrochemical water splitting.
We proposed a novel approach inspired by recent advancements in materials science to address the need for increased density of active components in electrodes. Building upon the utilization of additive CNTs and 3D-printed metal–organic frameworks/resins for enhanced electrode performance,9,22–24 our method employed printable chitosan and zeolitic imidazolate framework (ZIF)-67-containing ink to create polymeric scaffolds. By transforming this ink into a cobalt and nitrogen-containing carbon matrix, we eliminated the necessity for polymeric binders, thus streamlining the fabrication process. The density of the metal phosphides was precisely controlled by adjusting the cobalt and nitrogen content, linked directly to the ZIF-67 dosage, ensuring uniform distribution and optimal loading of active components. This addressed the issues of weak adhesion and limited active component loading observed in previous methods. Moreover, by introducing mesoporosity into the carbonaceous scaffolds, we enhanced access to metal phosphides. The combination of micrometer-sized pores between filaments and ZIF-derived micropores created hierarchical porous systems that significantly improved ion/charge and mass transfer. We envisaged that this comprehensive enhancement in electrocatalytic efficiency sets our approach apart from existing methods.
Herein, we present a novel approach utilizing extrusion-based 3D printing of chitosan-ZIF ink to create polymeric scaffolds, effectively trapping Ni-Co-P nanosheets. Optimizing ZIF-67 dosage (5.0 g) and introducing mesoporosity with P123 (0.2–2.0 g) [P123 = a symmetric triblock copolymer consisting of poly(ethylene oxide) (PEO) and poly(propylene oxide) (PPO)], yielded an elaborately fabricated electrode with exceptional electrochemical performance: It exhibited low overpotentials of 57 mV at 10 mA cm−2 and 263 mV at 500 mA cm−2 for HER, along with impressive stability over 1000 h. Additionally, it outperformed nickel foam (NF)-based electrodes, with a competitive overpotential of 163 mV at 10 mA cm−2 in 1.0 M KOH over 260 h. The electrode functioned efficiently as both anode and cathode for water splitting, achieving a voltage of 1.43 V at 10 mA cm−2 for 200 h. This outstanding performance stemmed from its hierarchical porous structure, facilitating efficient transport of electrons, ions, and gas bubbles, and the dense arrangement of anchored metal phosphides exposed more active sites, which accelerated the water splitting process.